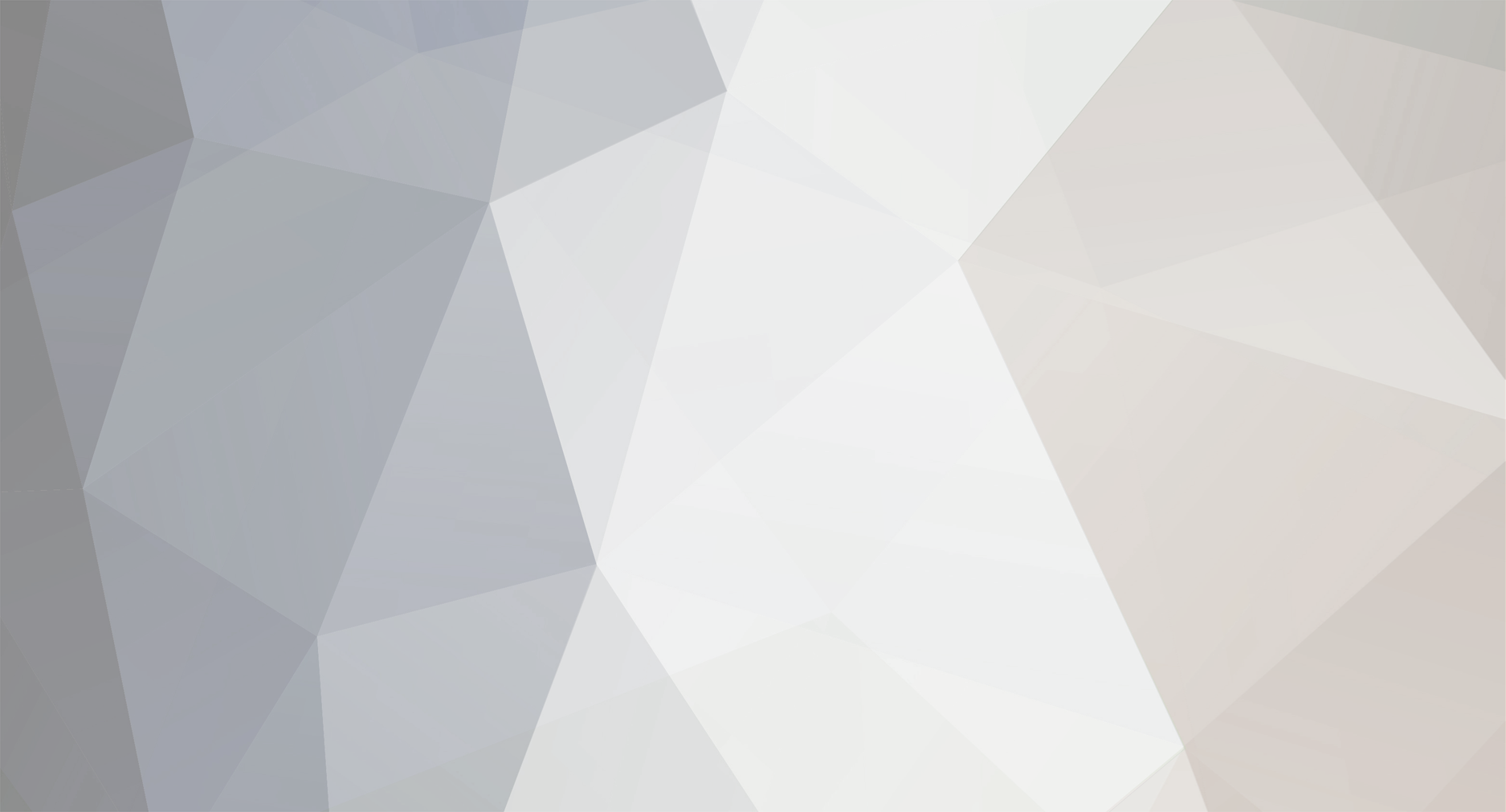
Jdude95
Members-
Posts
1,376 -
Joined
-
Last visited
-
Days Won
44
Everything posted by Jdude95
-
Thunder River Rapids Incident Coronial Inquest
Jdude95 replied to Jamberoo Fan's topic in Theme Park Discussion
The CCTV from the 2014 incident was shown again and this is the first time Mr Buss has ever seen it. A raft stops at the end of the conveyor, the conveyor is still moving and another raft comes down and bumps into it 4-5 times before the conveyor is stopped. Mr Buss cannot remember turning off the conveyor but states that if rafts were touching, he would have shut off the conveyor to prevent any issues. A few weeks after the incident, Mr Buss was interviewed and suspended without pay before being terminated. Mr Buss recalls the low air alarm being an audible alarm and a flashing light on the control panel. Mr Buss states that there is definitely a flashing light on the control panel for a pump failure alarm but cannot recall if there is an audible alarm. At the time of the incident, Mr Buss was one of the most senior ride operators at Dreamworld Mr Buss was shown a picture of the control panel and asked if it is the same as when he was operating the ride. Mr Buss states the only two new things added are a lockout device and a conveyor reset button. Mr Buss states that there are 2 conveyor stop buttons. A soft stop and an instant stop. The soft stop is generally issued for issues where the whole ride doesn’t need to be shut down. We have just been adjourned for today. Thank you for tuning in, I shall pick this back up tomorrow. -
Thunder River Rapids Incident Coronial Inquest
Jdude95 replied to Jamberoo Fan's topic in Theme Park Discussion
Stephen Buss Began at Dreamworld in 2006, was terminated in 2014 after an incident where he stopped the thunder river rapids ride which caused two rafts to collide. Mr Buss states that he was trained as a level 3 operator for every ride and was trained in every position on thunder river rapids. Mr Buss was fully trained on all roles on TRR in March 2008. Mr Buss states that training for the log ride and TRR was over 2 days where all other rides had a 1 day training. The trainer would shadow the trainee for the entire time they are training. Me Buss confirmed that trainers wouldn’t leave until they were confident that the trainee knew what they were doing. Mr Buss states that the level 3 operator is often quite busy due to a lot of multitasking that was required. Mr Buss was asked if it was a lot to deal with and if it was difficult, he stated that it got easier with more experience. The level 3 operator is in charge of monitoring every aspect of the ride from load and dispatch, queues, water levels, stuck rafts and even removing rubbish from recently emptied rafts. During training for the level 3 role, it’s generally not taught to be watching the conveyor and the spacing of the rafts as it’s already learned in the level 1 and 2 roles. Mr Buss was advised that during his time there, he was advised about maintaining the spacing between the rafts as that was one of the major things that needed to be monitored as he had heard stories before of a raft flipping but can’t remember where he heard this. Mr Buss states that Dreamworld management would drill into trainees that the spacing of the rafts is the most important thing to monitor on TRR. Mr Buss states that during his time there, staff would constantly be quizzed by management and trainers on safety procedures and other aspects of the rides they would look after. Mr Buss states that if there is an operational change to the ride, all staff must be signed off to say they have been trained in the new process. If a staff member got questions wrong during the quizzes, they would be taken off the ride and retrained. Mr Buss mentioned that the quizzes would occur a few times a year. Mr Buss was asked about alarms from the ride. The only alarm was the low pressure alarm which means a pump has stopped. The alarm is in place because the first raft in line needs to be tethered to the station so that it can’t float away as it is past the raft jacks in the station. Mr Buss states that the saying was “when in doubt, just stop the ride. When clarifying this, Me Buss stated that when that happened, you would shut off the conveyor as the e-stop only turns off the pumps and that would be no help. Mr Buss can never recall a time that he or another staff member have ever pressed the e-stop button on the unload platform. That button shuts off the conveyor and a pump. In the event of a low air alarm, all the jacks would automatically lower to allow all the rafts to come home. Mr Buss states there was a low air alarm, so he anchored the first raft in the station so it doesn’t float away. He didn’t realise there were 3 other rafts still in the course when he turned off the conveyor. For a bit of clarification, there were 2 alarms, a low air alarm and a pump failure alarm. During this incident, it was a low air pressure alarm. Which is a different process to a pump failure. During a pump failure, the process is to shut off the conveyor. During a low air alarm, the process is to anchor the first raft and then let all other rafts return home. Mr Buss states that he got confused as the low air alarm had fixed itself and forgot there were 3 rafts still on the course when he accidentally shut off the pump which caused a raft to bottom out at the end of the conveyor. Mr Buss didn’t notice that one had bottomed out at the start of the conveyor when he restarted the conveyor which caused the second raft to collide with the first one when it came over the conveyor. Mr Buss continued to operate the ride for the rest of the day and wasn’t even aware there would be an investigation into it until 1-2 weeks after. -
Thunder River Rapids Incident Coronial Inquest
Jdude95 replied to Jamberoo Fan's topic in Theme Park Discussion
Nigel Irwin Senior security control room operator Was a part time junior manager during the time of the incident. Mr Irwin is in charge of the security and communications control room. When a ride operator calls for assistance, it goes to the control room to be triaged out to the correct person. Mr Irwin also views the CCTV monitors. Mr Irwin is the staff member who contacted emergency services when the incident occurred. Mr Irwin received a call from the ride operators that a pump had shut down and he looked at the CCTV and confirmed that the south pump had failed. Mr Irwin recalled radio chatter between maintenance guys about a fault with the pump. The issue was then rectified and the ride was reopened. Mr Irwin states that it was a quiet day until the incident. Mr Irwin received at call at 2:06pm to call a code 222 blue which is a medical emergency. Mr Irwin asked for more details but the operator only stated that “I’ve got a raft on the conveyor” Mr Irwin wasn’t sure of the nature of the incident so he checked the CCTV and saw a raft on its side in the air and upgraded the call to a code 222 grey which is a medical emergency involving machinery. At the time, Mr Irwin observed that there was a raft at the end of the conveyor but no guests inside. The conveyor and pumps were stopped and the rapids alarm wasn’t sounding. Mr Irwin states that when first aid arrived onsite, they requested he call Queendland Ambulance. Mr Irwin then went over the radio to upgrade the call to a code 222 emergency which is the highest response level. During Mr Irwin’s call to Queensland ambulance, he states “we’ve had a mechanical failure on our rover rapids, we have somebody trapped in the machinery and after being told an ambulance is on its way, his response was “we may need more” Queensland Police came to view the footage in the control room and Mr Irwin had to view the CCTV footage over and over so many times as he needed to show ever new officer that arrived. Mr Irwin states that this was greatly distressing. Mr Irwin was asked if there were any improvements that he could think of to this process. “I think there should be an alarm for every ride and every issue so people know exactly what the issue is. The park also doesn’t have a PA system which would be helpful” Mr Irwin replied. Mr Irwin was asked if there was any difficulty or impairment in emergency personal accessing the site, to which he replied “no”. Senior management has their own radio channel to discuss situations like that. Mr Irwin filled in as the duty manager from time to time and they would report to the Operations manager. His role was primarily security duty manager. Mr Irwin would often work split shifts where he is in the control room half the day and a duty manager for the other half. This is due to the duty manager being at an advantage if he can view the CCTV monitors. Mr Irwin was asked about his training which was primarily done through shadowing with an experienced staff member. Mr Irwin also had additional training from the person who has the role before him. The Control room operator is generally hired from the pool of security staff that are excelling in their role and not hired without security experience. Mr Irwin claims responsibility for almost entirely eliminating bag theft within White Water World. Mr Irwin was also in charge of the control room on the day of the log ride incident. Where he said he learned a lot about how to react in an emergency situation. Mr Irwin states that the log ride and TRR emergencies both went smoothly, but unfortunately there was nothing that could be done for the victims when staff arrived. Mr Irwin states that he doesn’t recall a debrief for staff in the days/weeks after the event. He did have RDO’s during this period but was still not aware of any briefs that happened with staff. Mr Irwin is currently not working at Dreamworld as he is suffering from PTSD and has been since May 2017. Mr Irwin was not aware of any previous incidents on TRR or that there was any potential for rafts to flip. There are 2 main park wide alarms, the rapids alarm and the animal escape alarm. Mr Irwin was under the impression that the river rapids alarm was due to it being such a large unmonitored ride, not because there was such catastrophic potential. Emergency training has been implemented for staff post incident. Mr Irwin has mentioned that he would often receive calls that were not urgent as junior staff weren’t sure how to react in an emergency situation and he just needed to calm them down and inform them of the correct procedure. Mr Irwin states that the only emergency drill that he has ever undertaken in the park, was a bomb threat drill. Not a ride evacuation or any other emergency situation. Mr Irwin doesn’t believe there was any delay between contact from the ride op and contact of emergency services, he states that it would have been “3-4 seconds”. Mr Irwin was never provided with any reason as to why a code 6 breakdown folder was kept. Mr Irwin believes this folder was copied by Queensland police when they were gathering evidence. Each folder covers a full calendar year and then gets archived after the year is complete. Mr Irwin doesn’t believe the process of getting in contact with the control room could have been done any quicker. The only notification Mr Irwin got was the ride operator calling and saying “code 222 blue, I’ve got a raft on the conveyor” and then hung up. Mr Irwin then Checked the cctv monitors and upgrades the call when he say the raft sideways. Mr Irwin has just finished giving evidence. -
Thunder River Rapids Incident Coronial Inquest
Jdude95 replied to Jamberoo Fan's topic in Theme Park Discussion
It was briefly mentioned this morning that the staff will be perusing civil action but the front page of the courier mail today is the first time that the assisting legal team was made aware of it. Mr Cruz only accessed TRR documents stored on DW hard drives after the incident in 2016. Prior to this, those documents couldn’t be located. Mr Cruz has just finished giving evidence -
Thunder River Rapids Incident Coronial Inquest
Jdude95 replied to Jamberoo Fan's topic in Theme Park Discussion
Mr Cruz cannot remember viewing any urgent safety alerts from any ride manufactures in regards to updates or problems with the rides. Mr Cruz will take onboard all of the recommendations from the manufacturer including to shut the ride down if required. Mr Cruz was asked if part of his qualifications included building risk assessments but he cannot remember. Since 2016, risk assessments are completed by a number of people. Mr Cruz was not aware of the managers and general managers qualifications. Mr Cruz was not aware that the general manager was in charge of registering the rides. Mr Cruz has access to external companies in regards to engineering expertise. Members of external organisations had been working in the park prior to 2016. Mr Cruz tried to attend every weekly management meetings but was unable to make it to some. Safety was the first point on the agenda of those meetings and if a safety issues was raised, it would be addressed. We were then shown the annual mechanical and structural report for 2016 which was completed September 29, 2016 The only recommendation is to include the conveyor rollbacks as part of the daily check as the rollback gate at the top of the conveyor wasn’t working. Mr Cruz was asked if there were any documents that were required for this annual inspection that he couldn’t locate. His answer was “no”. Pitt and sherry were onsite days prior to the 2016 incident, inspecting the “big 9” but not TRR. Pitt and sherry are still performing audits, recommendations and development of rides at Dreamworld. After the closure of Dreamworld in 2016, Pitt and Sherry reviewed all the rides which were then re-reviewed by another company (LTC) before they could re open to the public. We have just adjourned for lunch and shall resume at 2:30 -
Thunder River Rapids Incident Coronial Inquest
Jdude95 replied to Jamberoo Fan's topic in Theme Park Discussion
CCTV Footage of the 2014 incident was shown. A raft stopped at the bottom of the conveyor, outside of the unload station, the conveyor kept operating and a another raft came in contact and the rafts were bumping until the conveyor was stopped. Mr Cruz had never had any discussions with senior team members about previous incidents on the rapids ride. Mr Cruz has not been trained to complete risk assessments, audits or safety procedures on rides. Until recently, DW mostly engaged outside companies to complete risk assessments as there was a lack of knowledge and expertise within the Dreamworld staff. Mr Cruz agrees that other DW maintenance staff should be shown the CCTV as it would be useful. Mr Cruz was asked if there was a culture of secretism around ride issues prior to 2016. Mr Cruz didn’t respond. Mr Cruz was in contact with an external expert when they were required to visit the park. Mr Cruz was asked if external organisations should be aware of he CCTV footage of incidents. He responded with “I don’t know” Mr Cruz was asked about Pitt and Sherry and advised that they were onsite in the days before the 2016 incident, completing audits on other rides. Mr Cruz was instructed to provide documentation to Dreamworld lawyers after the incident. Mr Cruz was asked if those documents were available to any staff members but he doesn’t believe so. Mr Cruz was tasked with developing an auditing tool. As part of this, he went to a WHS conference. He then worked closely with WHS and Dreamworld Management to develop this tool. During the 2016 annual maintenance Mr Cruz can’t remember having difficulty finding maintenance documents to provide to the annual maintenance auditor. Mr Cruz was then shown emails between him and the Auditor of the 2016 maintenance. It was then confirmed that he did have difficulty finding daily and annual inspection schedules and documents for some rides but not others. Mr Cruz has stated that he received 3 months of training and that includes being shown each ride and their operations. This included the daily inspections and maintenance programs for 90% of the rides. He was only officially trained on about 60% of the rides. Mr Cruz was explained prior to starting that there was an electronic system for determining preventative maintenance. Mr Cruz believes after that 3 months, he had a full understanding of all the rides and daily/weekly maintenance programs at Dreamworld. -
Thunder River Rapids Incident Coronial Inquest
Jdude95 replied to Jamberoo Fan's topic in Theme Park Discussion
The first witness for the day he just been called. Gen Cruz who began at Dreamworld in September 2014 as a mechanical engineer. Mr Cruz would approach Peter Gardner (a senior maintenance staff member) to raise any concerns about the ride. Mr Cruz and Mr Gardner were the only two people at the time who had formal tertiary qualifications. My Cruz was asked if there should be recourse management after the event of a critical incident, such as a near miss. Mr Cruz was not aware of two near miss incidents in 2014 on rides nor was he aware of the 2014 TRR raft collision that happened. He was only made aware of this, days after the incident when he located the risk assessment completed after the raft collision. Mr Cruz was shown photos from the 2001 raft collision and he agreed with barristers that there should have been changes made but he was not aware of the incident. Mr Cruz was never shown cctv footage of the 2014 incident as it still exists. Mr Cruz maintains that this is the first time he has heard of a raft collision incident in 2014 but doesn’t agree that it would have been helpful if he was made aware of the incident as risk assessments are not a part of his role. Mr Cruz was asked if there was someone who was made aware or in charge of any incidents when they occur in terms of recourse management. Mr Cruz’s response “I don’t know”. Mr Cruz then later agreed that it would be helpful for engineering staff to be shown CCTV footage of the 2014 incident, or any critical incidents that occurred. Mr Cruz states that when there is a near miss, it is a collaborate effort to perform recourse management. Sina (new engineer hired in 2017) was the only other person with formal engineering qualifications outside of Mr Cruz and Mr Gardner. We were then shown the termination letter of the 2014 staff member. During the 2014 incident, there was a low air alarm and the ride operator shut the ride down without checking where all the rafts where. This resulted in a raft bottoming out ontop of the conveyor, one floating into the reservoir, and another colliding with the raft in the conveyor, pushing it down the conveyor until the conveyor was turned off. The ride operator at the time was only aware of the raft in the reservoir when the photo shop called and informed them. At this point, the ride op escalated the situation to a code 6 but has not followed the procedure to initiate shut down. Which states that the ride much be shut down in any situation where there is a risk of seriously injury to guests or staff or damage to equipment. The ride op did not raise the rapid ride alarm but instead restarted the conveyor when there was a raft at the bottom that was at a large risk of flipping due to the increased water pressure. -
Thunder River Rapids Incident Coronial Inquest
Jdude95 replied to Jamberoo Fan's topic in Theme Park Discussion
Okay guys, so there has been an NPO (Non Publish order) for the things discussed during the first moments of today. One of the journos has already gotten into trouble for posting it. I’ll figure out what’s going on and then post the details from early today if I can. Essentially, Angus Hutchins, the Safety Manager for Ardent, has applied to give evidence sooner rather than later as his mental condition is deteriorating after witnessing the event and court will be a very stressful time for him. -
Thunder River Rapids Incident Coronial Inquest
Jdude95 replied to Jamberoo Fan's topic in Theme Park Discussion
Also, for anyone wondering, "Naumann" is pronounced as "Normon" -
Thunder River Rapids Incident Coronial Inquest
Jdude95 replied to Jamberoo Fan's topic in Theme Park Discussion
Mr Naumann can’t cant recall any times where a risk assessment is completed on a ride during its annual maintenance. Mr Naumann was asked if there were any maintenance issues from October 2015 to October 2016. Mr Naumann stated that there are always maintenance issues that occur or any ride. After an annual inspection a ride must be run a certain number of times and then signed off, this includes completing the daily maintenance checklist before the ride can return to service. During February 2016, an additional sensor was added at the start of the conveyor that would shut down the ride if a raft was sitting there for too long. Mr Naumanns role during this was to ensure contractors didn’t overlap when undertaking those works. Mr Naumann was asked if there was a person in charge of the maintenance and upgrades of the ride as there was no original manufacturer to refer to. Mr Naumann confirmed there was no one who undertook this role and stated that there should be someone in that position We have just adjourned for lunch. I unfortuantly won’t be here for the second half today. I’m having some family problems that I’ve got to take care of. Rest assured that I will be back again tomorrow and live posting again. Sorry for calling it early today but I hope my coverage so far was informative -
Thunder River Rapids Incident Coronial Inquest
Jdude95 replied to Jamberoo Fan's topic in Theme Park Discussion
Mr Nauman confirmed what aspects of the slats were checked during annual maintenance. If new slats were required, Mr Nauman would be the person to order the new slats. Mr Nauman states that in 2016 that the entire conveyor chain was replaced and the slats were removed and inspected. An independent company inspected the chain and advised the entire chain should be replaced but they did not assess the slats. Some of the slats were replaced during the chain replacement. Mr Naumann never inspected or looked at any other rapids ride types in Australia or internationally. During the chain replacement, the slats were then reinstalled and alternated between new planks and good condition old planks. Mr Naumann was asked about the engineering meeting where it was stated that “repairs and maintenance spending needs to stop, only CAPEX” Mr Naumann advised that this would have come from the general manager of maintenance. Mr Naumann became a qualified fitter/turner after he commenced his role at Dreamworld. Mr Neumann used to work for a foundry in a maintenance planning position. Mr Naumann isn’t aware of what the operators are and aren’t made aware of, in relation to maintenance issues. Mr Naumann was asked about an observation from WHS about corrosion in the construction of the rapids ride. The corrosion would have been there more than a year before the incident. Me Naumann advised it was “probably duly noted and scheduled for correction action when it could be done or when it could be afforded” Mr Naumanns role didn’t include making decisions on whether maintenance would occur based on whether it could be afforded. That decision was made by the finance department and the general manager of Engineering. If the maintenance issue was identified that raised concern about guest safety, the decision would not be made bu a single person. -
Thunder River Rapids Incident Coronial Inquest
Jdude95 replied to Jamberoo Fan's topic in Theme Park Discussion
Mr Murphy states that there is no pressure put on him or other maintenance members to get rides reopened as soon as possible. A ride will not open until the relevant maintenance person can inspect and repair the ride if needed. If an outside specialist I’d required, the ride will not re-open until they have also inspected the ride. A maintenance supervisor can arrange outside help without gaining approval from their manager. Mr Murphy’s understanding was that when there was a code 6 breakdown called for TRR, the procedure was to shut off one pump. Mr Murphy has just finished giving evidence. Grant Nauman Maintenance planner at Ardent Leisure(Dreamworld) Commenced role in April 2007 Qualified fitter and turner. Grants role is primarily administrative but has filled in as a maintenance supervisor when required. Mr Nauman wasn’t provided any training in regards to the national maintenance standards. Mr Nauman is not responsible for daily inspections. Mr Nauman was brought on to help implement the new electronic maintenance filing database. All maintenance requests will go into the electronic system unless it is determined as an urgent maintenance request. Each non urgent request had a work timeframe of around 7 days. Mr Nauman was in charge of ordering parts, labour and additional assets for a ride. Prior to 2016, a weekly checklist was generated by the Maintenance Planner with all outstanding work that was required. The work was then split up and allocated. Mr Nauman reported to the general manager of engineering. Mr Nauman no longer takes on the role as maintenance supervisor when staff is short. -
Thunder River Rapids Incident Coronial Inquest
Jdude95 replied to Jamberoo Fan's topic in Theme Park Discussion
The hearing starts early so I missed the first few minutes. Stephen Murphy Employed since 2013 Maintenance team leader/Fitter welder Responsible for a team of 4 mechanics. A pressure gauge would be used to check raft inflation pressure. TRR will be closed after 2 breakdowns within a day but there was a team leader meeting to change that to the ride closing after 3 breakdowns within a day. Mr Murphy can’t recall why it was changed. Previous employer had provided WHS training to complete risk assessments. No one ever raised an issue with the spacing of the slats on the conveyor. So it was never identified as a “pinch point risk”. A thunder river rapids alarm would warrant its own emergency response team. Other occurrences that require an emergency response team are the likes of an animal escape or a “code blue” medical emergency. Mr Murphy wasn’t aware of any previous incidents on TRR. A memo went out in early 2016 to TRR unload operators to be extra vigilant while monitoring he conveyor. Mr Murphy was not aware of this memo. The memo states that if there is an issue identified with the conveyor or brackets, to bring all rafts home. This would include bringing all rafts back through the “unsafe” conveyor into the unload station. Mr Murphy was never informed or aware of the incident in 2014 where a staff member was fired after shutting off a pump causing a raft to become stuck on the conveyor. Mr Murphy was shown an unlabelled e-stop on the control panel and he was not sure what the button did as he never used it. Part of the daily maintenance checklist was to inspect the conveyor but the e-stop at the unload area wasn’t checked daily. It was checked “occasionally” The e-stop on the control panel was never tested as it is not part of the daily checks as maintenance test the ride and not the controls. Mr Murphy stated that an e-stop is required by law to state that it is an e-stop but not what it actually does. The breakdown reports are kept at the main control panel for the ride. After a ride had the same fault 3 times within the one day, a supervisor will inspect and advise if the ride can reopen. The conveyor was checked daily for chain alignment, chain wear, slat alignment, slat wear but not if the slats were “bowed or warped” -
Thunder River Rapids Incident Coronial Inquest
Jdude95 replied to Jamberoo Fan's topic in Theme Park Discussion
Yes, I will be attending an live posting from the courtroom again. -
TOT Needed a new control system almost 10 years ago, they opted not to then. It would cost a lot more to do it now given the current state of the ride. They what? You realise it would be cheaper to buy and install a new off the shelf coaster? The cost of removing the old track, getting new track manufactured and then installed would be ridiculous. If they are going to the effort of re-tracking the ride, they may as well also rebuild the supports... and the station... and replace it with a new ride.
-
I can't see how they had such a limited space to work with when they pretty much demoed most of the building. I swear I remember the original plan being far less invasive to the theatre structure which is why there was capacity issues.
-
Well the e-stop isn't labelled so Dreamworld would definitely be the experts to call.
-
This is why I wont settle for anything less than an R rating for any spin-offs
-
They wanted a PG rated show. I couldn't settle for anything less than an R rating
-
Dreamworld Late September Update 2018
Jdude95 replied to Gold Coast Amusement Force's topic in Theme Park Discussion
Buzzsaw has the capability to do 2 full loops but this is mostly just done during testing and maintenance. It would be awesome if they bumped up the ride time and allowed it to complete the 2 full loops while guests are riding. -
Gold Rush to get aviation theme at Dreamworld?
Jdude95 replied to themeparkaddict's topic in Theme Park Discussion
Honestly, the only reason i'm excited about Buzzsaw potentially reopening is that I can get a look into the gold rush area without having to get on GD